- Главная страница
- Новости
- Бетонные реакторы токоограничивающие
Бетонные реакторы токоограничивающие




Идея использования токоограничивающих реакторов проста: потребление активной (полезной) мощности катушкой индуктивности минимальна, но её реактивное сопротивление суммируется с эквивалентным сопротивлением системы, что по закону Ома уменьшает токи в случае коротких замыканий. Уменьшение токов КЗ желательно по целому ряду соображений — позволяет уменьшить отключающую способность выключателей, стойкость оборудования к термическим и динамическим токам, уменьшить "толчок" энергосистеме в случае КЗ. В конечном итоге — позволяет снизить стоимость оборудования и повысить надёжность работы.
Первоначально, в качестве токоограничивающих использовались реакторы с масляной изоляцией. Но поскольку изготовление и эксплуатация большого бака с маслом чрезвычайно затруднительны, такие реакторы приходилось изготавливать с ферромагнитным сердечником (для уменьшения габаритов обмоток).
Быстро выяснились существенные недостатки таких реакторов — при токах КЗ с апериодической составляющей сердечник такого реактора насыщался, что приводило к снижению сопротивления реактора (то есть реактор терял свою функцию ограничения тока) и искажению формы кривой тока (что затрудняло действие устройств релейной защиты). Поэтому начался поиск других решений — реакторов с воздушным сердечником, которые бы оставались линейными в ходе любых переходных процессов. Отказ от масляной изоляции также был весьма желательным. Как в силу её пожаро- и взрывоопасности, так и для уменьшения объёмов технического обслуживания реакторов.
Поэтому, в 1950-е и 1960-е годы во всём мире шёл активный поиск технических решений в части сухих токограничивающих реакторов с воздушным сердечником. Было предложено две основных конструкции: с бетонным каркасом и с несущей обмоткой.
В СССР была принята конструкция с бетонным каркасом — так называемые бетонные реакторы. В англоязычной литературе эти реакторы известных как cast-in-concrete air-core reactor или cement hollow reactor. Первая версия ГОСТ "Реакторы токоограничивающие сухие", определяющих требования к этим реакторам, была введена в действие в 1970 году. Затем этот стандарт был заменён на ГОСТ 14794-79, который действует до сих пор. Актуальная версия стандарта ФСК СТО 56947007-29.180.04.165-2014 "Реакторы токоограничивающие на номинальное напряжение 6-500 кВ" во многом базируется на этом ГОСТ. Таким образом, бетонные реакторы играли и продолжают играть большую роль в энергосистемах Советского Союза и современной Российской Федерации.
Бетонные реакторы это комбинация конструкции и технологии изготовления. Получить аналогичные свойства аппарата с использованием других материалов или технологий изготовления весьма затруднительно.
Обмотка реактора изготавливалась горизонтальными слоями в виде спирали. Между витками обмотки предусматривались воздушные зазоры. Это делалось для увеличения уровня изоляции и для охлаждения и вентиляции обмоток. Механическая фиксация обмотки выполнялась бетонным каркасом, который изготавливался методом заливки на подготовленную обмотку. Делалось это так:
Многожильный провод укладывался в специальный шаблон. Шаблон предусматривал специальные отсеки — формы для заливки бетона. Такие отсеки имели прямоугольную форму и располагались радиально по отношению к обмотке. После укладки провода, в отсеки заливался электротехнический бетон высокого качества. После затвердевания бетона образовывался монолитный каркас, идеально облегающий провод обмотки. Вся конструкция тщательно высушивалась, дополнительно обрабатывалась лаком для защиты от влаги.
Бетонные реакторы в целом получились удачными. Бетон это материал, обладающий высокой прочностью, немагнитный и не проводящий электрический ток, что очень важно. Реактор в процессе работы создаёт сильное переменное магнитное поле, которое взаимодействует с любыми ферромагнитными материалами и электропроводящими предметами. Бетон нейтрален к электромагнитному полю и в этой связи идеально подходит в качестве материала каркаса реактора.
При заливке жидкий бетон плотно облегает провода обмотки точно повторяет их форму, что предупреждает образование точек концентрации механических усилий при прохождении больших токов через обмотку реактора. Благодаря этому механические усилия равномерно распределяются по всей конструкции реактора. Это, в сочетании с высокой прочностью бетона, обеспечивает стойкость к динамическим токам КЗ.
Также бетонный каркас не требует никакого технического обслуживания.
Практически 50-ти летний опыт эксплуатации бетонных реакторов в СССР, а затем и в России однозначно доказал их высокую надёжность и высокие эксплуатационные качества. Производство бетонных реакторов было освоено целым рядом предприятий СССР, они до сих пор эксплуатируются на сотнях объектов по всей территории России и бывшего СССР.
Вместе с тем, бетонные реакторы имеют объективные недостатки:
- Для их производства требуется обеспечить высокое качество бетона, стабильную технологию заливки и сушки. Необходимо обеспечить полное отсутствие трещин в бетоне. Поскольку в противном случае конструкция будет легко разрушена при прохождении токов КЗ.
- Бетонные реакторы изготавливались главным образом для внутренней установки. Так, как нагрев солнечной радиацией, перепады температур и осадки снижают срок службы бетонного каркаса.
- Бетонные реакторы обладали значительными габаритами и весом, что вело к сложностям при их монтаже и демонтаже.
- Сравнительно большие потери — за счёт большего рассеяния магнитного потока, что обусловлено геометрией обмотки.
Отдельной проблемой бетонных реакторов является жесткая зависимость между габаритами реактора и его номиналом (индуктивным сопротивлением). А увеличение номинала реактора приводит и к пропорциональному увеличению геометрических размеров его магнитного поля. Что требует переноса другого оборудования. Это ведёт к тому, что установить в существующую камеру бетонного реактора меньшего номинала новый бетонный реактор большего номинала часто оказывается невозможным.
В настоящий момент, хотя бетонные реакторы продолжают эксплуатироваться, они физически и морально устарели. Выпущенные в Советском Союзе реакторы полностью выработали свой ресурс. А современные электрические сети характеризуются значительно большими токами как нагрузки, так и короткого замыкания. Что требует больших номиналов токоограничивающих реакторов. А замена одного бетонного реактора на другой, большего номинала, может оказаться затруднительной. Даже при возможности физического размещения реактора в существующей камере возникают проблемы обеспечить требуемые расстояния между магнитным полем реактора и другим оборудованием.
Альтернативная конструкция реакторов — без каркаса, была разработана на Западе. Западные инженеры считали чрезмерно трудным обеспечить стабильное производство бетонных каркасов реакторов (хотя в СССР с этой задачей справились). А найти другой материал, который бы обладал свойствами, аналогичными электротехническому бетону, но был бы более технологичным, не удалось.
Первая успешная конструкция небетонного сухого реактора была предложена в 1950-х годах фирмой Spezielektra. Которая затем вошла в состав компании Trench, которая в свою очередь была куплена концерном Siemens. В 1962 году Тренч предложил конструкцию обмотки реактора, механическая прочность которой обеспечивалась за счёт её пропитки и заливки эпоксидной смолой. Такое решение позволило жёстко скрепить провода в обмотке — обмотка стала достаточно прочной, чтобы не нуждаться в каркасе.
Аналогичные по конструкции сухие реакторы без каркаса были затем выпущены рядом европейских и азиатских компаний либо на основе лицензии, либо на основе собственной разработки, заимствовавшей основную идею Spezielektra. В их основе общий принцип — выполнение обмотки в виде параллельных ветвей, каждая из которых представляет собой спираль, намотанную вокруг цилиндра. Ветви выполняются разного диаметра и устанавливаются в реакторе с воздушными промежутками по принципу матрёшки — самый маленький диаметр в центре, самый большой снаружи. Обмотки обжимаются сверху и снизу крестовинами, бандажируются, а затем пропитываются смолами или лаками. В результате образуется монолитная прочная конструкция, которая совсем не нуждается в каркасе.
Направление намотки обмоток монолитных реакторов — по спирали сверху вниз. Магнитное поле таких реакторов тороидальное, а разность потенциалов между слоями обмотки по горизонтали отсутствует. Это обеспечивает меньший уровень потерь, чем в бетонных реакторах и меньший стресс межвитковой изоляции.
Производство сухих реакторов с самонесущей обмоткой освоено и в России. Этим занимается компания КПМ. Её реакторы по своим характеристикам ничем не уступают реакторам зарубежного производства, являясь при этом полностью отечественным продуктом. На настоящий момент в эксплуатации находятся несколько тысяч фаз таких реакторов.
Прочность реакторов с монолитной конструкцией обмотки не уступает бетонным реакторам. Что подтверждено как испытаниями в независимых лабораториях, так и опытом эксплуатации. При этом, конструкция таких реакторов является более гибкой. Есть возможность, например, при равном номинале изготавливать реакторы меньшего диаметра большей высоты или наоборот. При равных с бетонным реактором размерах оказывается возможным обеспечить большие параметры — номинальный ток и индуктивное сопротивление реактора. Также реакторы с монолитной обмоткой не имеют ограничений на их эксплуатацию под открытым воздухом.
Современные монолитные реакторы самонесущей конструкции не только не уступают бетонным реакторам, но и во многом превосходят. В этой связи, использование монолитных реакторов вместо бетонных технически вполне оправданно.
В настоящий момент компанией КПМ накоплен большой успешный опыт замены бетонных реакторов на реакторы как в рамках аварийно-восстановительных работ, так и в рамках проектов ретрофит — увеличения мощности существующих объектов. Есть опыт реализации комплексных проектов — от разработки технических требований на замену бетонного реактора, до его монтажа и ввода в эксплуатацию. Это касается как токоограничивающих реакторов , так и реакторов специального назначения — например, пусковых .

Новости


Компании на карте
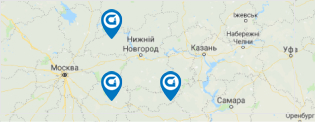
Вопросы и ответы
Мы писали заявку на продление разрешительного документа на ДТОиР в декабре 2018 года, нам тоже отказали. Почему отказали я не смог выяснить. Заказчик ...
Никто не обещал, что сертификация в СДС ИНТЕРГАЗСЕРТ - это легко и бюджетно! Если вы хотите поставлять продукцию в "Газпром" - никуда не ден...
Да вот непонятно, отменили или нет. Я создал новую тему по этому поводу....
Мы писали заявку на продление разрешительного документа на ДТОиР в декабре 2018 года, нам тоже отказали. Почему отказали я не смог выяснить. Заказчик ...